1、引言
在石油行业的原油管道输送过程中,各企业之间需要进行原油交接,因此流量计使用比较广泛。而计量精度则是一个关键参数,它关系到企业的经济效益和信誉。近年来,随着工业控制技术的飞速发展,可编程控制器(PLC)广泛进入工控领域,并增加了一些专用控制功能,例如PID调节功能、伺服功能、高速计数(HSC)功能等,又具有较高的可靠性,使得利用PLC实现原油自动计量就成为可能。为此,我们利用工业计算机(IPC)和PLC构成新型的集散式原油自动计量系统。此系统可通过以太网将数据远传至控制中心。
此项目已在鲁宁长输管线的数处计量站应用成功,在测量精度、系统稳定性、工作效率、可靠性及可操作性等方面,取得了良好的标定效果。
2、系统工作原理与硬件配置
2.1控制系统工作原理
系统结构如图1所示。运用管道输油时,通过现场控制室PLC打开/关闭相应的电动阀,进行流程切换,使相应的流量计投入运行。由流量计发信器将脉
冲传递到PLC,PLC利用高速计数模块采集流量计发出的脉冲数,并将其转换为标准状态下的容积值。同时,PLC将实时采集流体的压力和温度(分别由压力变送器和温度变送器提供),所有数据通过以太网送入上位IPC,IPC结合流体实时压力、温度值调用原油计量表数据库,将测得的累积量值转换为标准状态下(20℃,101325Pa)的累积量值,并将数据存储在IPC的硬盘上。而且,IPC可以驱动打印机打印出计量报告。
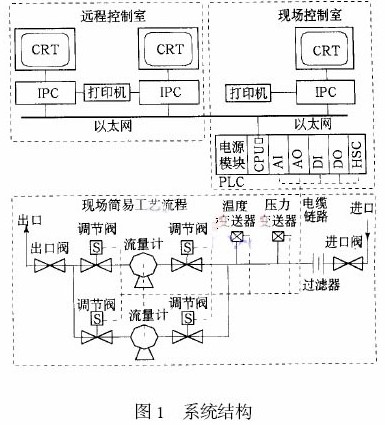
2.2控制系统的软、硬件配置
控制系统主要由一次设备、二次设备以及控制体和软件构成。一次设备主要包括压力表、温度计、流量计等;二次设备主要包括温度变送器、压力变送器、脉冲发信器、电动阀等;控制体主要包括PLC、IPC(配置网卡)、打印机、集线器及应用软件等,参见图1。
2.2.1硬件部分
(1)IPC:为保证系统的高度可靠性,选用了目前国内应用较多的DellGX260型计算机。具体配置为:PⅢ1.7GHzCPU、256MB内存、40GB硬盘、SONY21英寸纯平显示器、64MB显卡、声卡及音箱(报警和提示用)等。
(2)PLC:选用美国Rockwell公司的A2BPLC作为系统的控制核心,其特点是可靠性高、功能强、可扩展性好。具体配置如下:CPU为17472L551B(内置以太网通信口);模拟量输入(AI)模块选用17462NI4,它具有4个高电平模拟输入端,可输入4mA~20mA等标准信号,12位A/D转换精度,具有输入超调监控功能和测量滤波抗干扰功能;模拟量输出(AO)模块选用17462NO4I,它有4个模拟输出端,无需外部电源,可输出各种标准信号,包括0mA~20mA、4mA~20mA、±10V等信号;开关量输入(DI)模块选用17462I×16,它具有单端隔离的16路24VDC输入,所有的输入均配有滤波器,能够保证最大0.1ms的抗扰性,滤除线电源干扰;开关量输出(DO)模块选用17462O×16,它具有8路继电器输出,内部提供过载和短路保护,并具有通道故障自诊断功能;HSC模块选用17462HSCE,可计数最大频率为40kHz的脉冲,实现向上计数、向下计数或向上/向下计数。
(3)网络功能:根据设计中现场数据远程实时监视的要求,在每台IPC中各配置了1块网卡,PLC与IPC之间、IPC与IPC之间采用抗干扰能力较强的五
类屏蔽双绞线建立以太网。考虑到现场计量间距离调度室较远,在线路中间加入了3COM公司的8通道高速集线器,以保证数据可靠传输。
(4)流量仪表:采用日本OVAL公司的UF2Ⅱ型转子流量计,它具有精度高、流量范围宽、重复性好等优点。流量计现场部分配有不归零计数器和调整器,流量转换和变送部分为OVAL公司的PG30EP型脉冲发信器。
(5)温度压力仪表:温度变送器及压力变送器均能够提供4mA~20mA的标准信号。
(6)电动阀:可通过直流24V的开关量输出,控制电动阀的全开或全关,同时,电动阀提供无源的位置信号输出和状态信号输出。
2.2.2软件部分
系统的软件主要包括平台软件、PLC编程软件和IPC组态软件。
(1)系统平台软件:采用Windows2000作为系统平台,设置了系统密码和操作员指令,屏蔽了软件的某些功能,以限制系统的操作,防止非法用户进入系统。
(2)PLC编程软件:采用A2B公司的Rslogix500,它是一个基于Windows环境的编程软件套件,专供A2B500系列PLC使用,支持梯形图(LD)、指令语句表(IL)、顺序功能图(SFC)等多种语言模式,具有在线编程、诊断和在线仿真调试等功能,可支持以太网以及DF1FullDuplex、DH485、DF1HalfDuplexMarster/Slave等通信协议或通信总线。
(3)IPC组态软件:选用澳大利亚西亚特公司著名的工控软件Citect5.0,该软件可运行于WindowsNT/2000平台,具有采样速度快、实时性强、可靠性高等特点,组态方便,报警方式多样,实时、历史趋势曲线制作简单,能够与其它应用软件例如VB、VC、VF、Excel等实现无缝链接,灵活、方便地实现数据调用和报表打印。
3、控制系统的数据流向及软件流程
3.1数据流向
(1)PLC通过模拟量输入模块读取现场温度和压力数据(标准4mA~20mA信号),按仪表量程的不同,经程序运算转换为标准的工程量单位;通过高速计数模块读取流量计的脉冲信号,由主程序调用计量子程序,按照脉冲流量比计算出流量的瞬时值和累积值;通过控制开关量输入/输出模块电动阀的开关,来自动切换流程。
(2)IPC利用通信模块从PLC中读取数据,将其
记录到本机的历史数据库中,应用程序读取并显示现场数据及流量的瞬时值和累积值;同时,PLC也通过通信模块读取和执行IPC的操作指令。
(3)PLC将采集和计算得到的被检流量计各项参数传输到IPC,IPC结合流体实时压力、温度值,调用原油计量表数据库,将测得的累积量值转换为标准状态下的累积量值,由IPC调用Excel报表系统进行记录,驱动打印机自动打印出计量报表。
3.2软件流程
软件流程如图2所示。
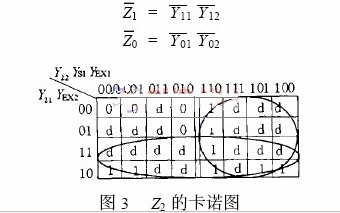
根据以上推导结果画出逻辑图如图4所示
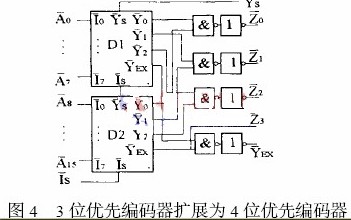
综上所述,在实现优先编码器的功能扩展时(以T4148为例),设计方法可归纳为:最高位片的使能输入端作为总的使能输入端,最低位片的使能输出端作为总的使能输出端,相邻两片之间,高位片的使能输出端接入低位片的使能输入端,总的扩展端?YEX为各片的扩展端逻辑“与”,总的代码输出中,低3位(Z2,Z1,Z0)为各片输出Y2、Y1、Y0逻辑“与”,高位输出端必须利用扩展端YEX来实现。当用4片T4148组成32线-5线优先编码器时,可按表4所示,列出扩展端与高位代码输出的真值表。
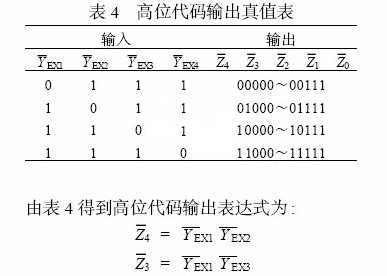
4、结束语
虽然本文讨论的是优先编码器的扩展设计方法,但是对于其它逻辑功能部件的扩展,也可依照同样的思路进行。