1 引言
大型风力发电机组中,风机叶片运行的稳定性直接决定着整个系统运行品质的优劣。在大型风力机复合材料叶片的生产过程中,叶片成型模具起着至关重要的作用。其中,叶片模具的温度是其加工成型过程中的重要工艺参数,对叶片成型模具的质量具有很大影响。如果温度控制的效果不佳,控制精度不高,控制系统的可靠性低,这些因素都将影响成型件的成型质量,甚至可能造成模具的局部烧损,导致模具失效,严重影响生产效率和产品交货周期。因此,模具加热装置的温度控制是风机叶片模具成型过程中的重要技术问题。它主要包括模具加热温度控制和模具温度均匀性补偿平衡控制[1-2]。
模块型plc具有配置灵活的特点,可根据需要选择不同规模的系统,而且装配方便,便于扩展和维修。针对叶片成型模具加热过程中区域划分多且复杂,在注胶固化,温控停止与合模固化过程中对温度的动态以及静态偏差要求严格的特点,设计了以欧姆龙cj1g-cpu45h-p模块型plc作为总控制器的叶片成型模具多路温度控制系统以实现流程控制,并且满足叶片模具成型的工艺要求。
2 叶片成型模具温控系统工艺要求
在感应加热,红外加热和电阻加热等加热方式中,对叶片模具加热来说,电阻丝加热具有元件经久耐用、维修更换方便、操作简单、成本低廉等优点。电阻丝加热就是在模具的玻璃钢层中预埋加热电阻丝,加热电阻丝铺设在模具加热层(树脂+铝粉)之下[3]。电阻丝加热方式虽然应用较普遍,但是随着风力机组容量的增长,风力机叶片的尺寸随之增大,兆瓦级大型风力机叶片模具的加热系统具有划分区域多且复杂的特点,在这一背景下,基于电阻丝加热方式的模具加热系统就显得缺乏可靠性,温度不易控制,易出现局部温度过高的现象,因此对于叶片成型模具的温度控制系统就提出了更高的工艺要求。
具体言之,对于兆瓦级大型风力机叶片模具而言,一般情况下要求模具型腔内加温能力至少为80℃;模具型腔恒温控制精度为±2℃;模具型面温度偏差不大于4℃(指模具温升动态过程)。成型过程的期望温度曲线如图1所示。
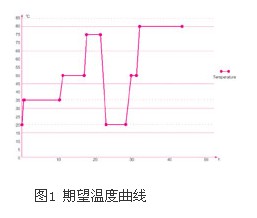
3 欧姆龙模块型plc简介
欧姆龙c系列plc产品门类齐,型号多,功能强,适用面广。其紧凑型结构的微型机以cj型机最为典型。经过筛选,欧姆龙cj型机中的cj1g-cpu45h-p型cpu单元适用于风电叶片成型模具的多路温度控制。
cj1g-cpu45h-p作为cpu单元的模块型plc的可靠性高,抗干扰能力强,并且适用于多路温度控制。cj1g系列plc所具有的温度控制单元支持2回路或4回路pid控制或on/off控制,其中2回路模式带加热路断路检测功能;同时用于pid控制的pid常数可以用自调整(at)来设定,正向操作(冷却)或反向操作(加热)可以任选;可以从温度传感器直接输入;采样周期为500ms;每个回路有2点内部报警;对于2回路模式,电流互感器接到每个回路,用来检测加热器的断路。
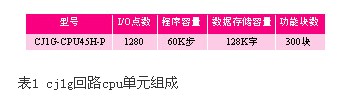
4 多路温度控制系统设计
4.1 系统体系结构
由于叶片成型模具是分为多个回路进行加热的,故在一个总控制器用于协调各路加热温度的基础上,每个单回路则分别进行各自区域的温度采集以及对温度场的加热,恒温保持与冷却工作。整个系统的控制原理图如图2所示。

该多路温度控制系统应主要具有4个方面的基本功能,即实时控制功能、显示功能、数据处理功能、报警和故障处理功能[4]。根据上述系统的主要功能,对该多路温度控制系统的总体结构进行设计,系统总体结构示意图如图3所示。整个温度测控系统的硬件包括数据采集模块、输出控制模块、热电阻、固态继电器、人机界面及总控制器等。下面分别从温度传感与采集,总控制器以及执行机构三部分介绍该系统整体体系结构。

(1)温度传感与采集
以单区温度测量为例,每个单区的型腔内设置两个测温点,每个单区的控制点温度测量使用2个欧姆龙公司的e52-p10ae型pt100热电阻,测量的最高温度可以满足温控系统的工艺要求,由于叶片成型模具型腔内测温不导电,故pt100无需安装绝缘套管。同时,采用pt100型热电阻测温可以有效避免采用热电偶作为传感器所产生的冷端补偿误差,提高温度测量的精确度。4通道输入模块cj1w-ad04u进行温度数据采集。
(2)总控制器
该多路温控系统采用欧姆龙公司的cj1g-cpu45h-p模块型plc作为总控制器来协调控制所有单回路的温度。该plc具有内置回路控制功能的cpu单元,可以直接实现多段温度及斜率控制。根据模具温控系统所要实现的功能,用户系统需要对以下内容进行程序开发:动画显示,编制控制策略,输出实时曲线、历史曲线、实时数据、历史数据,操作界面和菜单设计,外部设备连接,运行测试等。
(3)输出控制模块与执行机构
该系统采用16通道输出控制模块cj1w-od211通过g3na-410b型固态继电器分别控制各单区电阻加热丝的通断。g3na-410b型固态继电器可适用的输出负载为240-480vac,可以满足系统工作电压的要求。
该多路温度控制系统的主要控制元件选型清单见表2。所配备的控制装置最多支持68个单回路的温度控制。
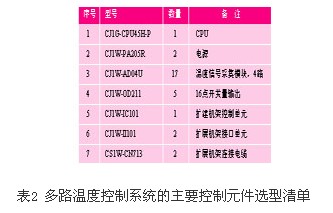
4.2 流程控制的设计
该控制系统的实现通过在欧姆龙工控组态软件
cx-programmer上进行应用系统开发来完成。基于组态软件开发的用户应用系统,其结构由主控窗口、设备窗口、用户窗口、实时数据库和运行策略5个部分构成。具体成型过程的控制流程示意图如图4所示,由图4可知,通过传感器测量和温度采集模块采集到的各单回路实时温度值均存入实时数据库,用户在主控窗口中调出实时数据库即可观察到各单回路的当前温度值,从而对温度异常点做出相应的处理。温度采集模块与输出控制模块的运行状态可以通过设备窗口得知。与此同时,图4中叶片模具成型过程的每一个阶段里,温升与恒温保持等流程均以相应的控制策略存储在应用系统中,即在每一阶段运行相应的控制策略以实现预期的成型流程。用户通过用户窗口可以得知当前成型过程所处阶段的系统状态,当用户窗口出现图4中所示的报警信息时,用户可以根据所显示的报警信息手动进行各通道的加热升温、冷却降温、恒温保持、启动和停止等一系列动作。最终使每一个阶段的成型过程满足工艺要求。用户应用系统5个部分具体的结构组成如下。
系统框架在主控窗口中构建。实时数据库是系统核心,用于管理所有的实时数据。该系统中共建立了140个数据对象,包括4个系统内建数据对象、最多支持68个单回路,共136个温度控制点的实时温度数据和加热冷却的温度控制阀值、开关型的控制参数以及组对象等。这些数据对象根据其实现功能的不同分别被赋予不同的属性。
设备窗口中定义了数据采集模块cj1w-ad04u和输出控制模块cj1w-od211,数据采集模块的4个通道分别与温度控制点实时温度数据连接,输出控制模块的16通道与加热及冷却的开关型控制参数相连接。
用户窗口用于实现数据与流程的可视化。主界面显示当前的温度值、设定的模具型腔恒温控制精度,模具型面温度偏差以及当前的控制状态;设计了曲线显示窗口分别显示每个温度控制点和组对象的实时曲线和历史曲线;温度控制点设置和温度运行控制窗口通过hmi的实时显示后可以供操作员手动进行各通道的加热升温、冷却降温、恒温保持、启动和停止等一系列动作。每个单回路在工控组态软件中的控制逻辑组态图见图5。


4.3 控制策略与精度分析
由于对所有单回路都要实时保持着准确的测量、pid控制和良好的人机对话接口,所以必需要有一套合理的控制算法。对于图4中所示的控制流程通过定义相应的运行策略来实现。对于每一路的电阻丝加热或冷却进行单独控制的时间循环通过设计如下的循环策略并编写脚本程序实现,当控制点初始温度小于所处阶段的加热阀值时,启动加热;当实测温度值达到该阶段的加热阀值时,相应的固态继电器断开,停止加热。模具的保温主要通过运行报警策略控制电阻加热丝的开关得以实现。
与此同时,由于pid只能输出mv值,即0~100%的模拟量信号,在控制系统中使用了cj1g-cpu45h-p模块型plc的tpo指令作为占空比计算工具,即可将对应的mv值转换为开关量的开关on/off状态,从而实现了对执行机构的控制。
对于实时温度测量传感器而言,本温控系统采用的e52-p10ae型pt100精确度属于b级,它的测量温度误差δt=±(0.3+5×10-3t),因此其测温误差足以满足±0.7℃的温度测量误差要求。同时由于系统设计的中断控制程序能够保证对所有单回路进行控制操作的实时性,所以可以满足叶片模具成型过程中各分区型腔内对温度±2℃的静态偏差要求以及模具型面温升过程中不大于4℃的动态偏差要求。
占空比系数是根据测量值与设定值的偏差大小、加热速率确定的,偏差越大,占空比越大,加热时间就越长[5]。待下次的测量值出现,重新调节占空比,直到达到恒温阶段,这个时候系统的加热/冷却达到平衡。若恒温过程中出现干扰时,如环境突然的变化破坏了恒温阶段平衡,此时系统会自动地调节占空比,使之重新达到平衡。
4 结束语
本文将欧姆龙plc应用于风电叶片成型模具多路温度控制当中,所设计的控制系统结构稳定,成本低廉,安全可靠。以欧姆龙模块型plc及相应外围元件构成硬件环境,以pid为基本控制算法的支持软件,对多路温度的测量、流程控制与控制算法进行了有效的设计,保证了测量、控制的实时性,不会因为路数过多而影响控制精度。可以有效解决温升与恒温过程中各区之间温度不均匀的问题。分析结果表明,cj1g-cpu45h-p模块型plc可以满足对叶片成型模具多路温度的控制要求,在相关领域具有良好的应用前景。